How AI Can Help in Inventory Management Software in the Logistics Industry
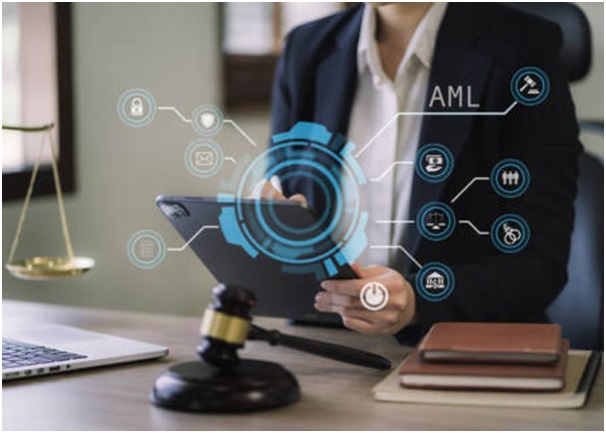
Inventory management has long been one of the most operationally intensive and cost-sensitive areas in logistics. From balancing stock levels to anticipating demand, reducing waste, and optimizing warehouse space, the process is both vital and complex.
Traditionally, logistics businesses have relied on static models, manual audits, and rule-based software to manage these moving parts. But with shifting consumer behavior, globalization, and the need for real-time responsiveness, legacy systems are no longer sufficient.
This is where Artificial Intelligence (AI) is making a meaningful impact. By enhancing the intelligence of inventory management software, AI is helping logistics companies automate, predict, and optimize inventory control with unprecedented accuracy and speed. The result isn’t just efficiency—it’s competitive advantage.
Let’s explore how AI is transforming inventory management software in logistics, how it works, where it adds the most value, and why it’s quickly becoming indispensable to modern supply chain operations.
The Limitations of Traditional Inventory Management
Most logistics operations today still use rule-based inventory management systems that rely on historical averages, manual inputs, or basic automation rules. These systems typically:
- Lack real-time visibility across warehouses, suppliers, and distribution networks
- Struggle to respond dynamically to demand spikes or disruptions
- Rely heavily on human intervention and guesswork
- Operate in silos without integrated forecasting, purchasing, or transportation modules
In high-volume, fast-moving supply chains, this can lead to overstocking, understocking, poor warehouse utilization, increased carrying costs, and customer dissatisfaction.
AI addresses these pain points by learning from real-time and historical data to predict demand, optimize reorder points, automate replenishment, and adapt dynamically to changing variables—without relying solely on human input.
Core Applications of AI in Inventory Management
Demand Forecasting
AI-powered systems analyze past sales, seasonal patterns, promotions, weather conditions, economic signals, and external data (like news or social trends) to generate demand forecasts that are far more precise than static models. This reduces guesswork and enables data-backed inventory planning at granular levels—SKU, store, and region.
Predictive Reordering
Instead of setting static reorder points, AI can analyze real-time inventory levels, vendor lead times, logistics constraints, and consumption trends to determine the optimal time to reorder. This predictive replenishment reduces the chances of both stockouts and surplus inventory.
Warehouse Optimization
AI algorithms optimize the layout of storage units, shelf space, and picking routes within the warehouse. Machine learning can analyze the frequency of item movement and adjust placement accordingly, ensuring faster picking and better space utilization. Vision-based AI also assists with real-time inventory verification through drones or cameras.
Inventory Categorization and Prioritization
AI tools segment inventory based on value, velocity, or customer impact—allowing logistics managers to apply differentiated service levels. For example, fast-moving or high-value SKUs may trigger automated alerts or receive priority handling.
Real-Time Visibility Across the Supply Chain
AI integrates data from various points—suppliers, in-transit shipments, warehouse sensors, and order systems—to provide a live, unified view of inventory. This helps managers track shortages, delays, or misalignments and take proactive steps.
Returns and Reverse Logistics
AI helps predict return rates, identifies patterns behind returns, and optimizes restocking or liquidation processes. This is particularly useful in sectors like eCommerce where return volumes are high and affect inventory planning.
Risk Detection and Disruption Response
By analyzing supply chain news, supplier performance, or geopolitical indicators, AI systems can detect potential inventory risks before they become problems—helping logistics companies adjust procurement strategies and reduce exposure.
Integration with Autonomous Systems
In advanced warehouse settings, AI works in tandem with robots, AGVs (Automated Guided Vehicles), and drones to track stock movement, initiate cycle counts, or move goods based on predicted demand.
How AI-Enabled Inventory Management Works
AI enhances traditional inventory management systems by adding layers of prediction, automation, and self-learning. The process typically includes:
- Data Collection: From ERP systems, WMS (Warehouse Management Systems), sensors, IoT devices, and historical records
- Data Processing: AI engines clean and normalize this data across locations, formats, and systems
- Pattern Recognition: Machine learning algorithms analyze data for trends, demand cycles, anomalies, or repetitive patterns
- Decision-Making: AI recommends actions—reorder points, supplier changes, or layout adjustments
- Automation: Integrated systems execute changes automatically (e.g., reorder with suppliers, reallocate inventory between sites)
This closed-loop system becomes smarter over time. The more data it processes, the better it becomes at identifying inefficiencies, improving forecasts, and reducing waste.
Business Benefits of AI in Inventory Management
Lower Inventory Costs
AI reduces the need for excessive safety stock and improves procurement precision. This lowers storage, insurance, and capital costs without risking stockouts.
Higher Service Levels
Fulfilling customer orders on time and in full becomes easier with accurate forecasts and proactive stock planning. This directly impacts customer satisfaction and brand loyalty.
Improved Operational Efficiency
AI removes bottlenecks and manual tasks in inventory control—freeing up human resources to focus on higher-value work like strategy and analysis.
Data-Driven Decision Making
Instead of reacting to problems, logistics managers can anticipate and resolve them before they disrupt operations. This shift from reactive to predictive decision-making improves agility and resilience.
Fewer Lost Sales
With real-time insights and better forecasting, companies can reduce stockouts and avoid missed sales opportunities—especially during peak seasons or demand surges.
Scalability
As businesses expand into new regions, channels, or product lines, AI systems scale easily—handling increased complexity without proportionate growth in operational overhead.
Risk Mitigation
Early warning signals powered by AI allow for risk-aware procurement and inventory strategies. This helps businesses navigate supply chain shocks, transportation delays, and vendor issues more confidently.
Midway through adopting AI in logistics inventory systems, companies often pair the strategy with Transportation software development to build fully connected ecosystems that manage not only stock levels but the flow of goods across routes, fleets, and destinations—ensuring complete operational alignment.
Challenges to Consider
While the potential is significant, businesses must also account for:
- Data quality: AI depends heavily on accurate, complete, and up-to-date data
- System integration: Connecting AI engines to existing WMS, ERP, and procurement systems requires technical coordination
- Change management: Teams need training and process alignment to trust and act on AI insights
- Initial investment: Building or adopting AI solutions involves upfront cost and effort, though ROI is often realized within 12–24 months
Successful AI implementation is rarely about plug-and-play tools—it requires strategic alignment, a clear understanding of KPIs, and a technology partner with domain expertise in logistics and supply chain systems.
Future Outlook: AI-First Inventory Systems
Looking ahead, inventory systems in the logistics industry will increasingly become autonomous, cloud-native, and deeply integrated with edge devices and analytics platforms. AI will shift from decision support to decision automation—handling replenishment, dynamic safety stock adjustment, and even supplier negotiations in real time.
Advanced systems will continuously balance cost, speed, sustainability, and service level—making trade-offs that align with business priorities. AI will also power sustainability initiatives by minimizing overproduction, reducing transportation emissions through better stock placement, and enhancing product lifecycle visibility.
The competitive frontier in logistics will be defined by how intelligently companies can move and manage inventory. Those leveraging AI to build connected, intelligent systems will be the ones shaping the next generation of efficient, resilient supply chains.
Final Thoughts
AI is not just enhancing inventory management—it’s redefining how logistics companies plan, respond, and grow. By embedding intelligence into stock control systems, businesses gain more than operational efficiency—they gain the ability to make smarter, faster, and more proactive decisions across the entire supply chain.
Whether it’s improving demand forecasting, automating replenishment, or ensuring warehouse agility, AI is becoming a core pillar of modern logistics operations. Organizations that act early, invest thoughtfully, and partner strategically will unlock significant value—not just in cost savings, but in resilience and long-term growth.
In the evolving landscape of logistics, intelligent inventory management is no longer optional—it’s a competitive necessity.