Smart Ways to Maintain Your Bevelling Machine for Peak Performance
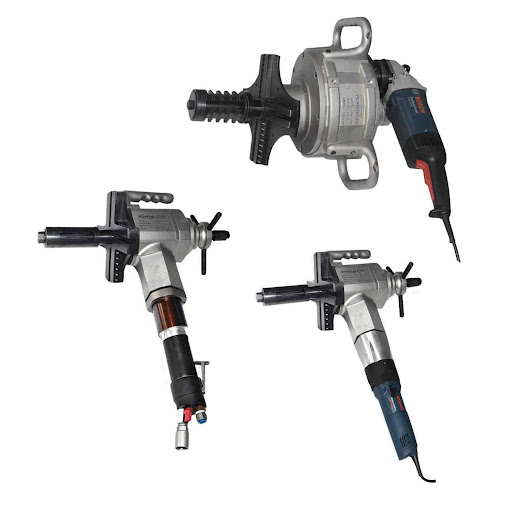
Bevelling machines are the unsung heroes of metal fabrication, pipe preparation, and welding operations. These powerful tools create precise angled edges on pipes, plates, and structural components, making them essential for achieving clean welds, perfect fits, and high-quality finishes. Whether you’re working in shipbuilding, construction, oil & gas, or heavy manufacturing, maintaining your bevelling machine is crucial to ensuring consistent performance, safety, and longevity.
Just like any precision tool, a bevelling machine is only as good as the care it receives. Neglecting maintenance can lead to breakdowns, poor-quality cuts, increased wear and tear, and even safety hazards. On the other hand, a well-maintained beveller delivers smooth, accurate edges and operates efficiently for years.
In this article, we’ll walk you through effective ways to maintain your bevelling machines so it stays reliable, sharp, and ready to tackle even the most demanding tasks on your job site or workshop floor.
1. Clean the Machine After Every Use
The simplest maintenance step is often the most effective. After each use, clean the machine thoroughly to remove metal shavings, dust, oil, and residue. These particles can get into moving parts, dull cutting tools, and even damage internal mechanisms over time. Use compressed air or a soft brush to clean hard-to-reach areas, and always wipe down external surfaces.
2. Lubricate Moving Components Regularly
Like any mechanical system, your bevelling machine relies on smooth, friction-free movement to operate efficiently. Check the manufacturer’s manual for recommended lubrication points, and apply the correct type of oil or grease at regular intervals. Pay special attention to spindles, gears, bearings, and sliding surfaces. Proper lubrication minimizes wear, reduces heat buildup, and extends the life of critical components.
3. Inspect and Replace Cutting Inserts or Blades
The quality of your bevel depends heavily on the condition of the cutting tools. Dull or damaged blades can cause rough finishes, inconsistent angles, and overloading of the motor. Regularly inspect cutting inserts or blades for signs of wear, chipping, or deformation. Replace them as needed, and always use OEM (original equipment manufacturer) parts to ensure the best fit and performance.
4. Check Power Cords, Cables, and Connectors
Whether your bevelling machine is electric or pneumatic, a secure and undamaged power connection is essential for safe operation. Routinely inspect power cords for cuts, frays, or exposed wiring. Ensure all connectors are tight, clean, and corrosion-free. If your machine is air-powered, check hoses for leaks or brittleness and replace them as necessary.
5. Monitor and Adjust Alignment Settings
Bevelling machines rely on precise alignment to create uniform bevels. Over time, vibrations or improper handling can throw the machine out of alignment. Check the guide rails, rollers, and cutting head for alignment accuracy before each major job. Many machines include adjustment screws or calibration marks to help you maintain proper settings.
Maintaining a tube beveling machine is not just about preserving a piece of equipment—it’s about protecting your workflow, your people, and your results. By following the 10 strategies outlined above, you can prevent breakdowns, maintain cutting precision, and get the most out of your equipment. Whether your beveller is cutting pipe edges for welding or preparing structural components for fabrication, these tools thrive when treated with care and attention.